The Ultimate Checklist for a Leak-Proof Metal Roof Installation
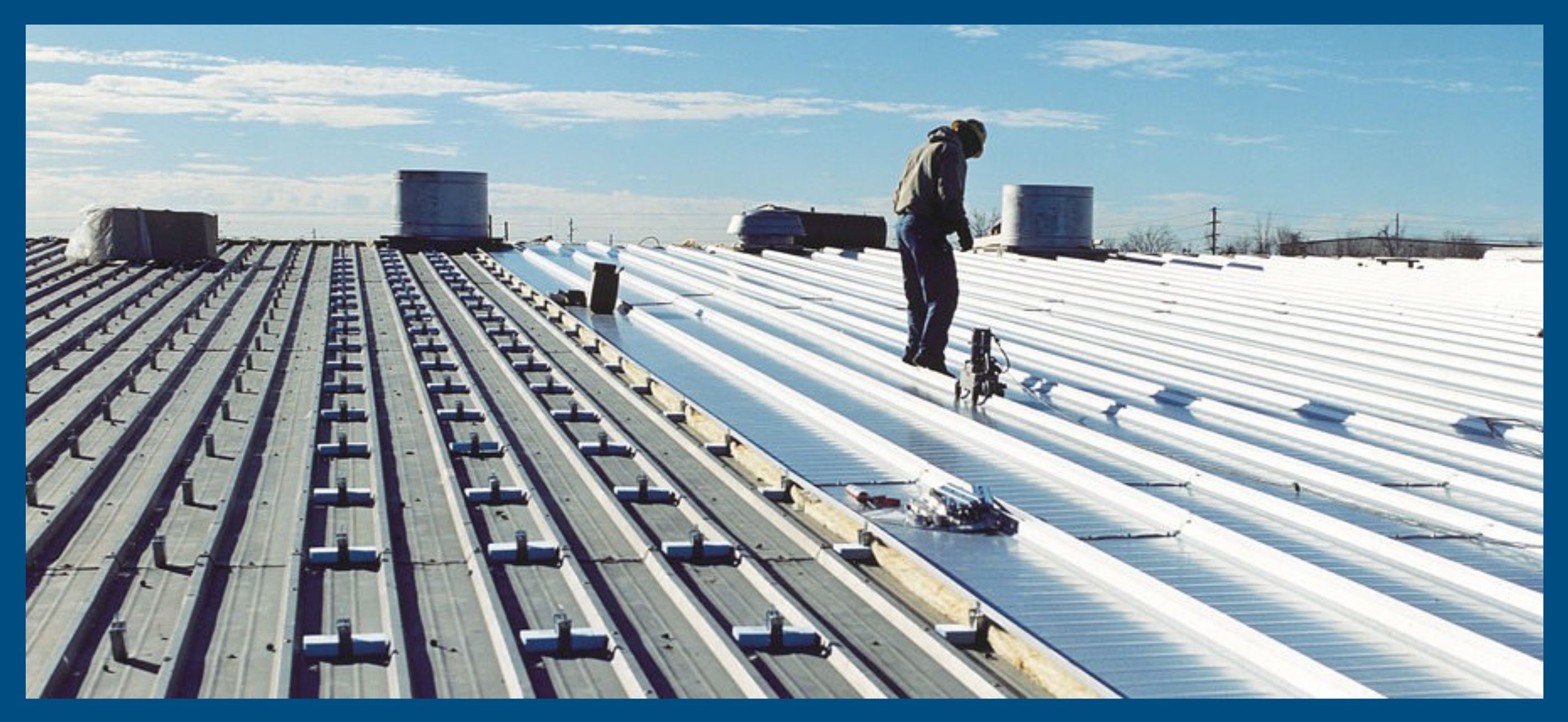
A well-installed metal roof can last for decades, but leaks often occur due to poor installation, not the materials themselves. Whether you're a contractor, builder, or property owner, following proper installation steps will help ensure your roof stays leak-free for years to come. In this guide, we'll break down the 10 essential steps to installing a metal roof that can withstand rain, snow, and harsh weather conditions.
1. Choose the Right Butler Roof System for Leak Prevention
Not all metal roofing systems are the same. Choosing the right one for your building makes a big difference in performance.
- MR-24® Standing Seam Roof - The best option for long-term leak resistance. Uses a Pittsburgh Double-Lock Seam that prevents water from seeping in.
- Butlerib II® Exposed Fastener Roof - A cost-effective option that requires extra sealing at fastener points.
- CMR-24® Insulated Metal Roof - Designed with insulation and thermal breaks to prevent condensation buildup, which can lead to hidden leaks.
Key Considerations: Choose a system based on building location, climate, and wind load requirements.
2. Design for Proper Roof Slope & Drainage
A metal roof must be designed to quickly shed water to avoid pooling, which leads to leaks.
- Minimum slope recommendations:
- MR-24®: 1/4:12 slope (best for low-slope applications)
- Butlerib II®: 1/2:12 slope (requires additional drainage planning)
- Install proper gutters and downspouts to direct water away from the building.
- In areas with heavy snow or rainfall, consider adding snow guards and diverters to prevent ice buildup.
3. Use Factory-Punched Panels for Perfect Alignment
Precision is critical for a leak-proof roof. Butler's factory-punched panels ensure proper alignment and fastener placement.
- Eliminates human error from manual drilling.
- Ensures seam width consistency, preventing gaps where water can enter.
- Factory pre-drilled holes prevent misalignment, which could lead to fasteners being improperly seated.
4. Secure Panels with the Right Fasteners & Sealants
Using the correct fasteners and sealants prevents leaks from forming at connection points.
- Scrubolt™ Fasteners - High pull-out resistance, preventing loosening over time.
- Lock-Rivet™ Fasteners - Used in overlap seams to hold panels tightly together.
- Sealants:
- Panlastic® Ribbon Sealant - Installed along panel seams for a watertight barrier.
- Cartridge-Based Panlastic® Sealant - Applied around fasteners and panel laps for added protection.
- Fastener Torque Requirements:
- Scrubolt™: 80 in-lbs
- Lock-Rivet™: Hand-tight plus ½ turn
5. Prevent Condensation with Proper Insulation Techniques
Condensation can lead to water damage and mold growth inside the building. Proper insulation prevents this issue.
- ThermaLiner™ Insulation System reduces moisture buildup inside the roof assembly.
- Stapling insulation tabs ensures a continuous vapor barrier.
- Use double-faced tape to secure insulation and eliminate air gaps.
- Vapor barriers prevent moisture from reaching cold metal panels, which can cause condensation.
6. Follow Proper Panel Seaming & Overlap Techniques
Seaming is a critical part of metal roof installation. A poorly seamed panel will allow water to seep in.
- For MR-24® Roofs:
- Use a Roof Runner® Seaming Machine to create a Pittsburgh Double-Lock Seam.
- Ensure the seamer follows the panel installation closely to avoid loose seams.
- For Butlerib II® Roofs:
- Overlap panels by at least one corrugation.
- Fasten panels at the valleys, not the peaks, to prevent stress cracking.
- For all roofs:
- Apply butyl tape at seam edges before fastening.
- Stagger end laps to prevent material buildup.
7. Ensure Correct Clip & Expansion Joint Placement
A metal roof will expand and contract with temperature changes. If clips and expansion joints are incorrectly installed, the panels may shift, creating gaps and leaks.
- Floating clip systems (used in MR-24®) allow for natural panel movement without stressing the seams.
- Expansion joints are required every 200 feet to accommodate metal movement.
- Incorrectly placed clips can restrict panel movement, leading to buckling and premature leaks.
8. Install Roof Penetrations & Openings with Weathertight Curbs
Any holes in the roof (for vents, skylights, or HVAC units) must be properly sealed to avoid leaks.
- Use seamed-in roof curbs, not standard flashing, for a weathertight fit.
- Apply Panlastic® sealant around curb edges and inside joints.
- Use counterflashing to shield curb edges from wind-driven rain.
9. Conduct a Final Leak-Prevention Inspection
Before finishing the installation, perform a thorough inspection to catch potential issues.
- Pre-installation checks:
- Verify all panels are aligned correctly.
- Ensure all fasteners are properly seated.
- Post-installation quality control:
- Perform a water test by spraying controlled water over the seams.
- Use a hand-held seam probe to check for incomplete seams.
- Common leak-prone areas to check:
- Panel overlaps
- Ridge caps
- Roof-to-wall transitions
10. Plan for Long-Term Maintenance & Re-Roofing
Regular maintenance extends the life of a metal roof and prevents future leaks.
- Annual inspection checklist:
- Tighten any loose fasteners.
- Check seams for movement or separation.
- Clear debris from gutters and downspouts.
- Metal-over-metal re-roofing:
- Butler’s Metal-Over-Metal Retrofit System allows for re-roofing without tearing off the old roof.
- Reduces downtime and eliminates the risk of exposure to weather during re-roofing.
Wrapping Up
A leak-proof metal roof starts with proper installation. By following these 10 essential steps, builders can ensure that the roof remains durable, watertight, and long-lasting. Whether using MR-24®, Butlerib II®, or CMR-24®, these best practices will help prevent leaks and maintain the integrity of the roof for decades.
For expert guidance and high-quality Butler parts, contact Butler MFG Parts today!